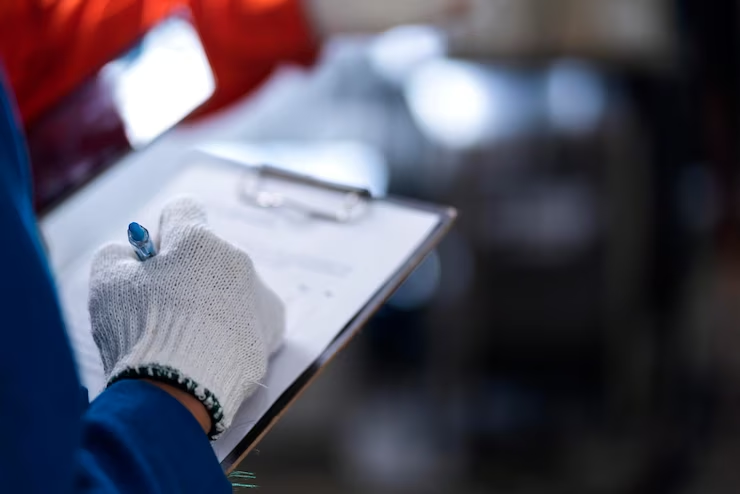
As the demand for custom plush stuffed toys only continues to grow, it’s essential for manufacturers to maintain high-quality standards to ensure customer satisfaction and business success. One way to achieve this is by conducting factory audits, which are essential to ensure that factories adhere to quality control measures, ethical manufacturing practices, and safety regulations.
This article will delve into the significance of factory audits for custom plush toy manufacturers, the benefits they provide, and the best practices to follow.
Whether you’re a toy designer or a retailer, understanding the importance of factory audits can help you make informed decisions and ensure that your products meet the highest quality standards.
By partnering with a reputable and experienced plush toy manufacturer, you can be confident that your custom plush toys are produced ethically and sustainably, ensuring your business thrives in today’s competitive retail market. So, let’s dive in and explore the significance of factory audits in ensuring quality and trust for custom plush toy manufacturers.

II. What is a Factory Audit?
Factory audits are a comprehensive evaluation of a manufacturer’s operations and are critical to ensuring that they meet the required standards for quality, safety, and ethical practices. There are several types of factory audits, including:
Social compliance audit: This type of audit focuses on a manufacturer’s compliance with local labor laws, working conditions, and worker rights. Examples of social compliance audits include SA8000, BSCI, and WRAP.
Quality systems audit: This audit evaluates a manufacturer’s quality control processes, including raw material inspection, production processes, and product testing. Examples of quality systems audits include ISO 9001 and ISO 14001.
Security audit: This type of audit assesses a manufacturer’s security measures, such as fire safety, equipment maintenance, and emergency preparedness. Examples of security audits include the C-TPAT and AEO certifications.
Environmental audit: This audit evaluates a manufacturer’s environmental impact, such as energy consumption, waste disposal, and pollution prevention. Examples of environmental audits include ISO 14001 and EMAS.
Product-specific audit: This audit assesses a manufacturer’s compliance with specific product requirements, such as toy safety regulations or food contact materials. Examples of product-specific audits include Sedex SMETA and ICTI CARE.
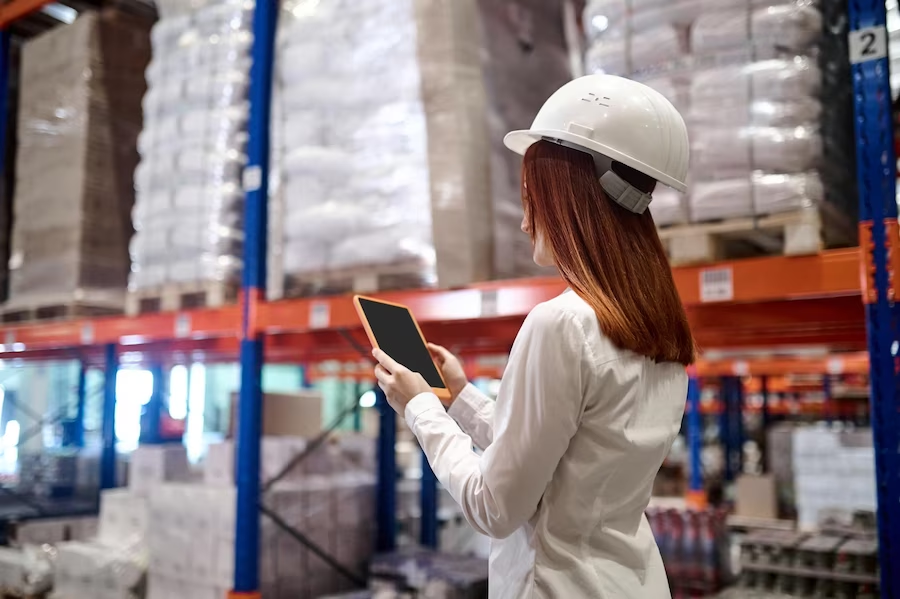
Each audit has its own set of standards and guidelines, and the type of audit required depends on the product being manufactured and the client’s specific requirements.
By conducting regular factory audits, manufacturers can identify areas for improvement and take corrective action to ensure that their operations meet the highest standards of quality, safety, and ethical practices.
In addition to the factory audits mentioned above, there are pre-production and in-process audits. Pre-production audits occur before the production process starts.
In contrast, in-process audits are conducted during production to ensure the manufacturing process is on track and producing products according to the required standards.
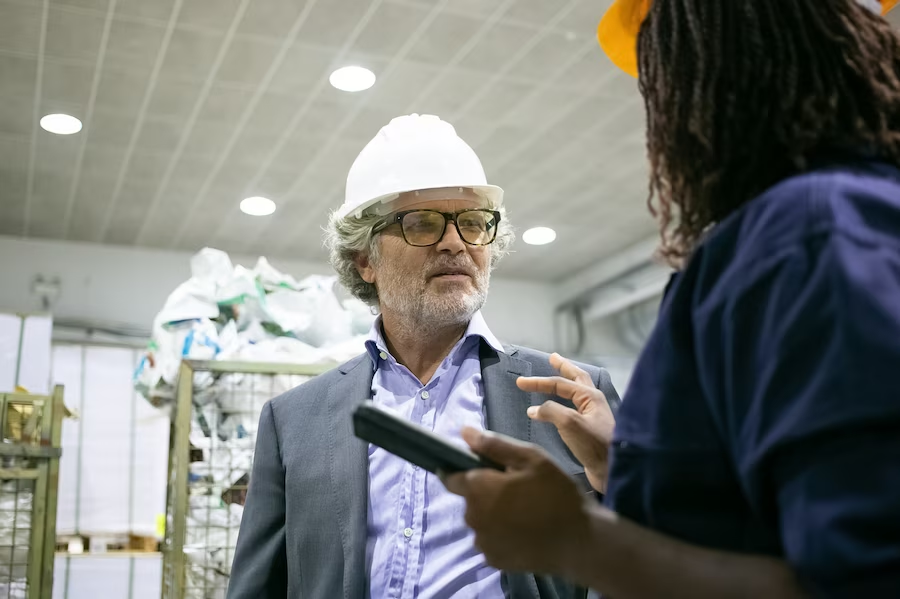
Pre-production audits involve checking the manufacturer’s capabilities, production process, and facilities to ensure they meet the client’s requirements.
In-process audits ensure that the production process meets the required quality standards, and any issues that arise can be addressed promptly to prevent further mass production of defective products.
Factory audits ensure manufacturers comply with legal regulations and industry standards. For example, if a manufacturer produces toys for children, they must comply with specific toy safety regulations to ensure that the toys are safe for children to play with.
By conducting regular factory audits, manufacturers can ensure that they comply with these regulations, avoiding any legal issues or recall that may arise from non-compliance.
Moreover, factory audits also help manufacturers build trust and credibility with their clients. By demonstrating their commitment to quality, safety, and ethical practices, manufacturers can differentiate themselves from their competitors and establish a reputation as a reliable and trustworthy partners. This can increase business opportunities, repeat customers, and create long-term partnerships.
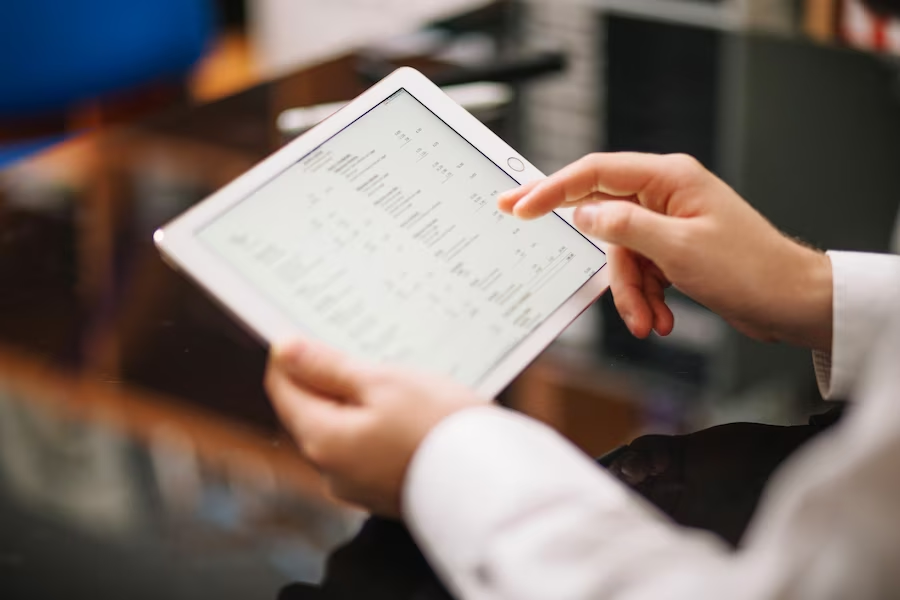
Overall, factory audits are critical in ensuring that custom plush toy manufacturers meet the required standards for quality, safety, and ethical practices. By conducting regular factory audits and addressing any issues that arise, manufacturers can improve their operations, comply with legal regulations and industry standards, and build trust and credibility with their clients.
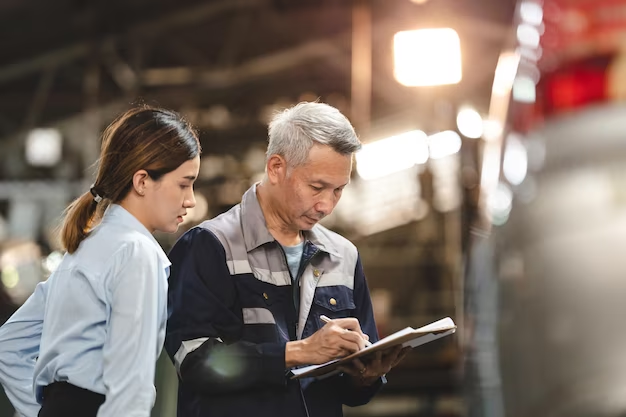
III. Why are Factory Audits Important for Custom Plush Toy Manufacturers?
Custom plush toy manufacturers need to ensure that their products meet the highest standards of quality, safety, and ethical manufacturing practices. Conducting factory audits is a critical step in achieving these goals. Here are some reasons why factory audits are important for custom plush toy manufacturers:
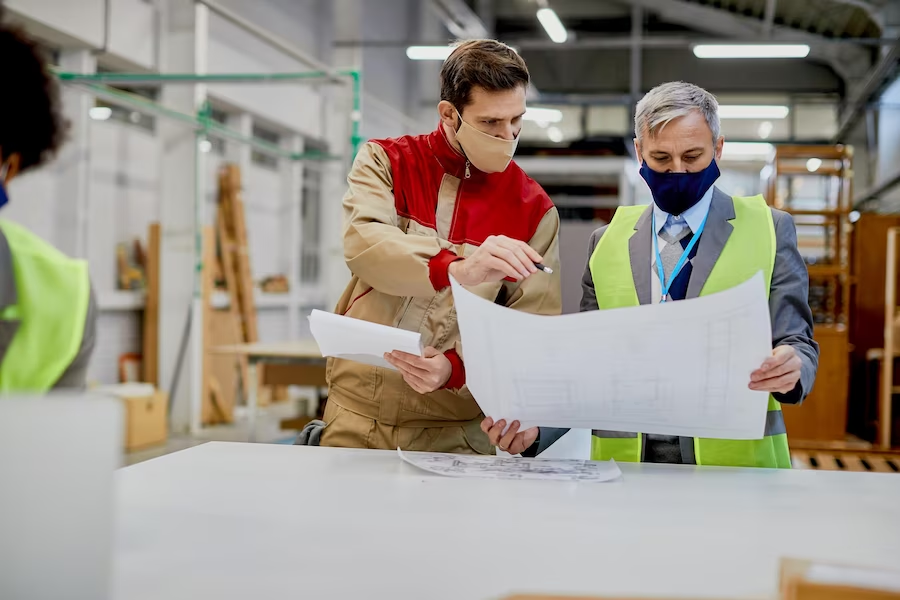
A. Quality Control
Factory audits help to ensure that the quality of products being produced meets the standards set by the manufacturer and their clients.
Auditors will check for compliance with specifications and identify any defects in the manufacturing process that could affect the quality management system final product. Manufacturers can maintain consistent quality and ensure customer satisfaction by identifying and correcting any issues early on.
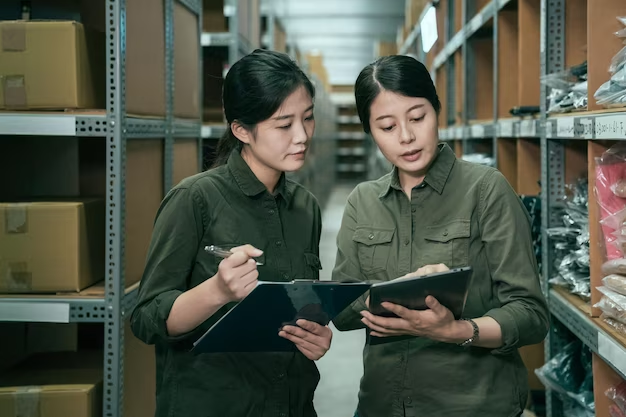
B. Safety
Plush toys are often intended for children, so safety is a top priority for custom plush toy manufacturers. Factory audits can help the toy industry ensure products are free from harmful materials and meet relevant safety standards, such as ASTM F963 and EN71. Auditors will check that proper testing is being carried out, that the materials being used are non-toxic, and that the finished product does not pose any risks to children.
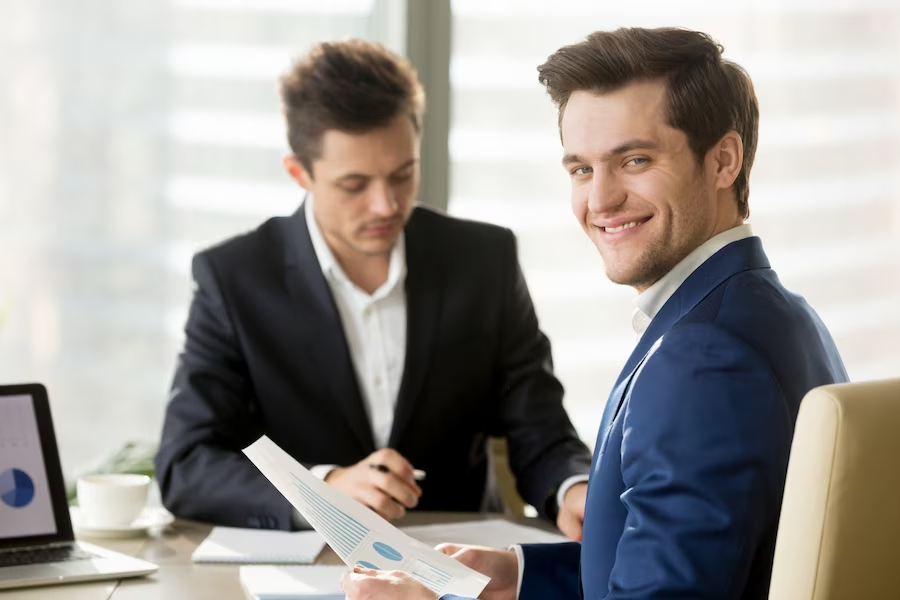
C. Ethical Manufacturing Practices
Consumers today are increasingly concerned about ethical manufacturing practices, such as labor conditions and environmental impact. Factory audits can help ensure that manufacturers operate ethically and comply with labor laws, such as child labor and fair wages. Auditors will also check that manufacturers use environmentally friendly practices, such as recycling and reducing waste.
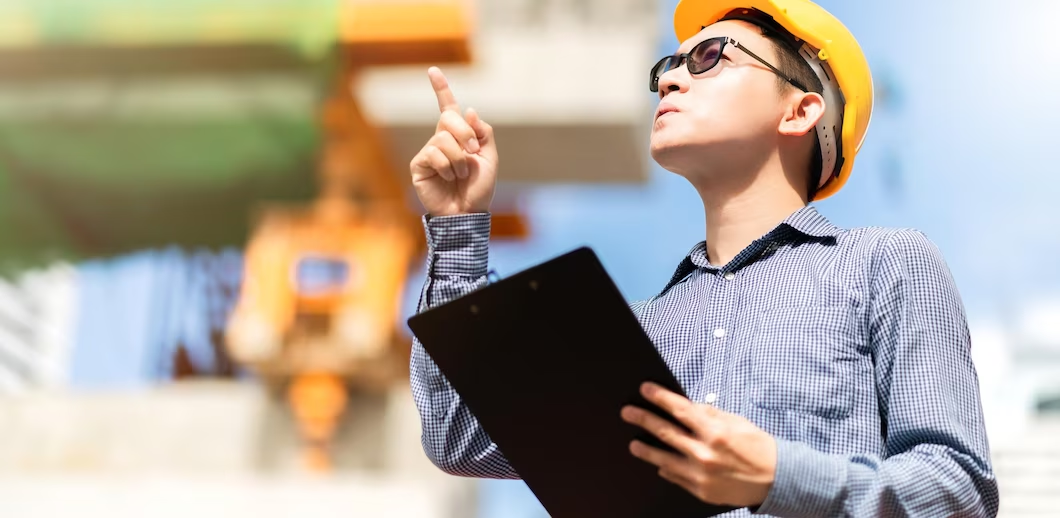
D. Supply Chain Transparency
Factory audits can provide transparency in the supply chain, which is important for manufacturers and their clients. Auditors will check that the materials being used are sourced from reputable suppliers and that no unauthorized subcontractors are involved in the manufacturing process. This can help to reduce the risk of supply chain disruptions and ensure that the final product meets the manufacturer, vendor’s, and clients’ specifications.
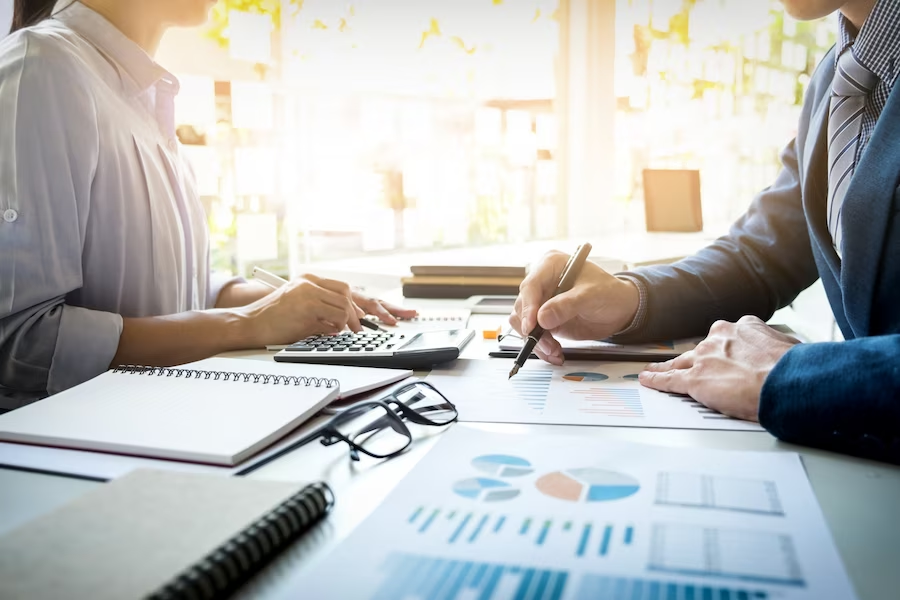
E. Compliance with Regulations
Manufacturers must comply with relevant regulations and standards in their industry, such as those related to safety and labeling. Factory audits can help ensure that manufacturers comply with these regulations and are aware of any changes that may affect their operations. This can help to avoid costly penalties and legal issues down the line.
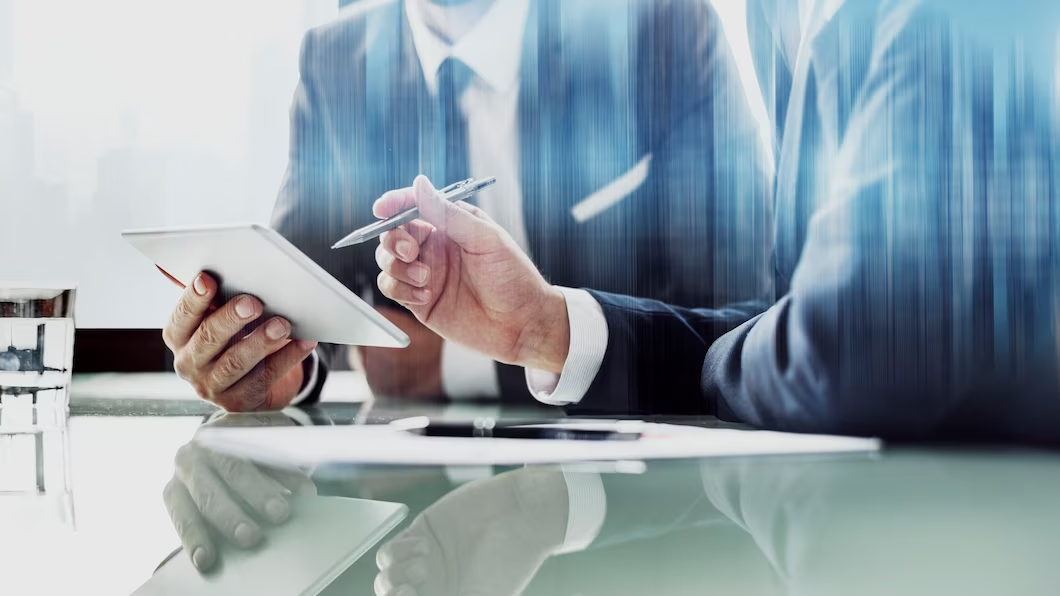
Overall, factory audits are essential for custom plush toy manufacturers to maintain quality, safety, and ethical manufacturing practices. By conducting regular audits, manufacturers can identify and address any issues early on, ensure compliance with regulations and standards, and maintain transparency in their supply chain.
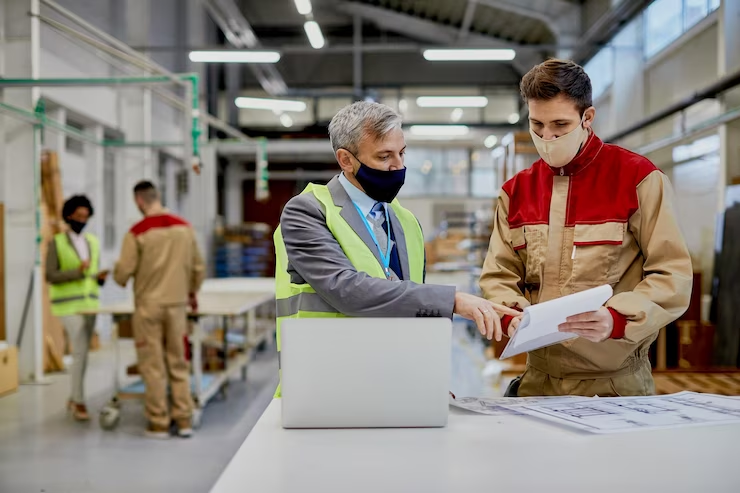
IV. What are the Benefits of a Factory Audit for Custom Plush Toy Manufacturers?
While conducting factory audits may seem like an added expense and hassle, it can actually provide numerous benefits for custom plush toy manufacturers. Here are some of the key advantages of manufacturing audit:
A. Improved Quality Control
Factory audits’ primary benefits are that they help manufacturers maintain strict quality control measures throughout production. By assessing the factory’s facilities, equipment, and processes, auditors can identify potential areas of concern and suggest improvements to ensure the final products meet high-quality standards.
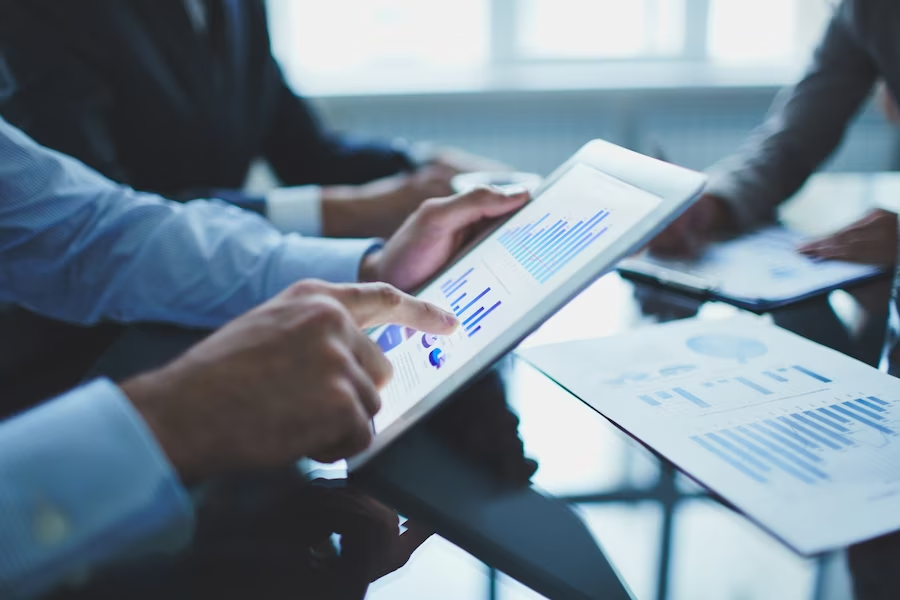
B. Ensuring Ethical Practices
Factory audits also play a critical role in ensuring custom plush toy manufacturers operate ethically and socially responsibly. Auditors assess the factory’s compliance with various international regulations and standards, including those related to labor, health and safety, and environmental protection.
This helps to ensure that the manufacturer is adhering to ethical business practices and protecting the well-being of the brand, its workers, and the environment.
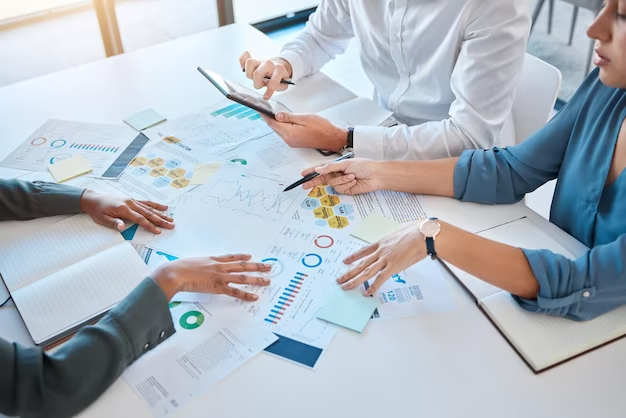
C. Enhancing Trust and Credibility
Factory audits also help to enhance a manufacturer’s trust and credibility in the eyes of clients, suppliers, and stakeholders. By demonstrating a commitment to quality, safety, and ethical business practices, manufacturers can differentiate themselves from competitors and build stronger relationships with customers and partners.
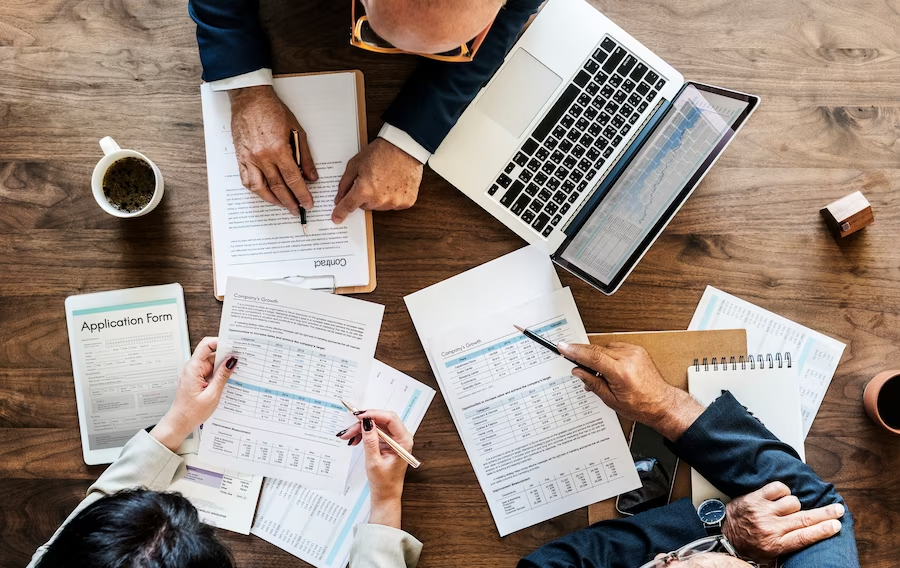
D. Mitigating Risks and Liabilities
Conducting factory audits can also help manufacturers mitigate risks and liabilities associated with quality issues, safety hazards, and ethical violations. Manufacturers can avoid costly legal battles, product recalls, and reputational damage by proactively identifying potential problems and taking corrective actions.
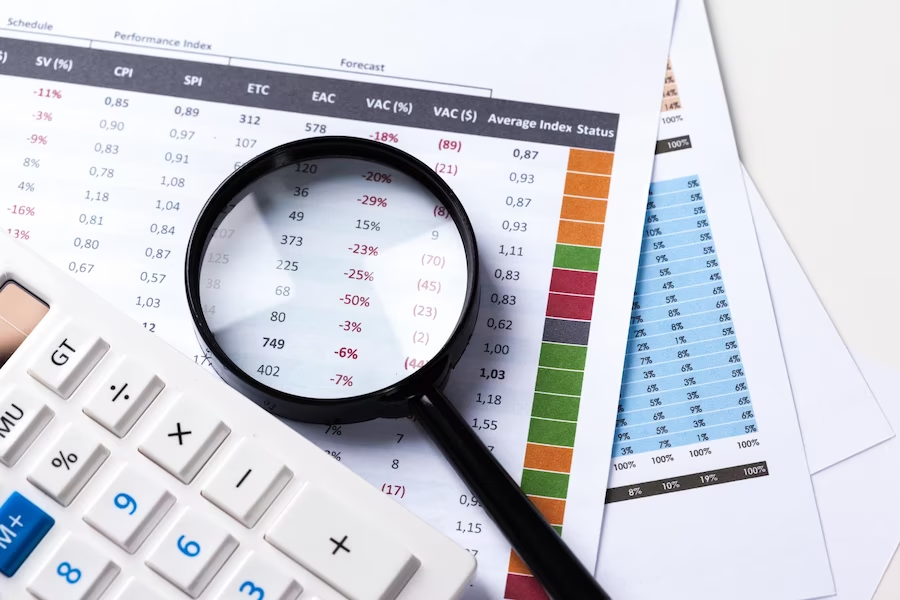
E. Improved Production Efficiency
Factory audits can also identify opportunities to improve production efficiency and reduce costs. By assessing the factory’s production processes and equipment, auditors can identify bottlenecks and suggest improvements to increase output and reduce waste.
Overall, factory audits are valuable for custom plush toy manufacturers looking to ensure they produce high-quality products, ethical business practices, and develop strong relationships with clients and partners. While they may require an upfront investment, the long-term benefits are well worth it.
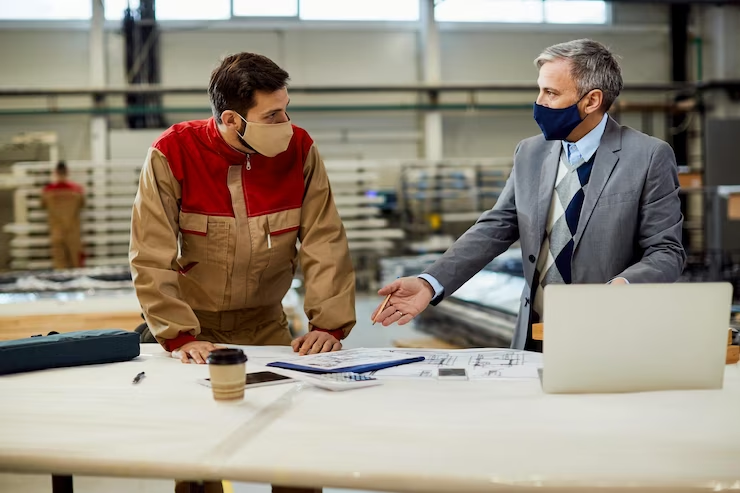
V. How to Prepare for a Factory Audit
When preparing for a factory audit, there are several key steps that custom plush toy manufacturers should take to ensure a successful and productive audit process. These steps include:
1. Establishing Clear Standards:
Establishing clear standards and expectations for your manufacturing processes before undergoing a factory audit is essential. This includes everything from safety protocols and quality control measures to ethical sourcing practices and environmental sustainability efforts. By clearly defining your standards and expectations, you can ensure everyone in your organization is aligned and working towards the same goals.
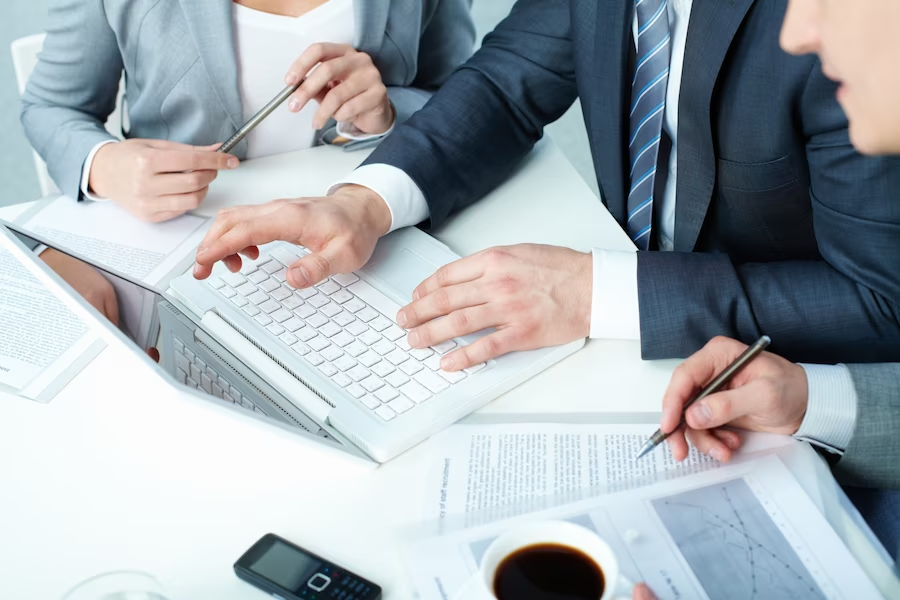
2. Conducting Internal Audits:
Before an external factory audit, it’s important to conduct internal audits to identify any areas of weakness or non-compliance. This involves reviewing your manufacturing processes and procedures, as well as your documentation and record-keeping practices. By conducting internal audits, you can identify and address any issues before they are flagged during an external audit.
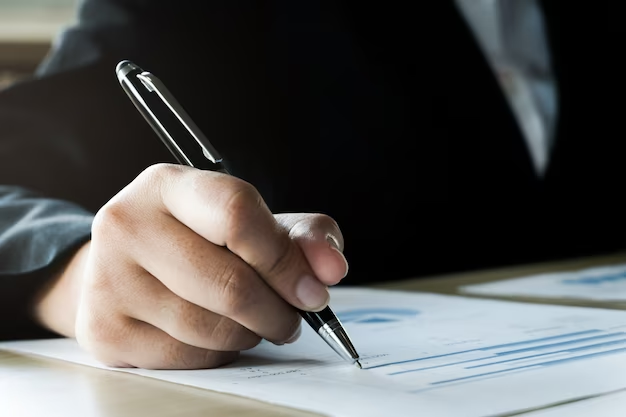
3. Training Staff:
Your staff plays a critical role in the success of a factory audit. Training your staff on the audit process, what to expect, and your standards and expectations are important. This includes training on safety protocols, quality control system, management systems and control measures, ethical sourcing practices, and environmental sustainability efforts. Ensuring your staff is well-trained and prepared can demonstrate your commitment to meeting high standards and achieving compliance.
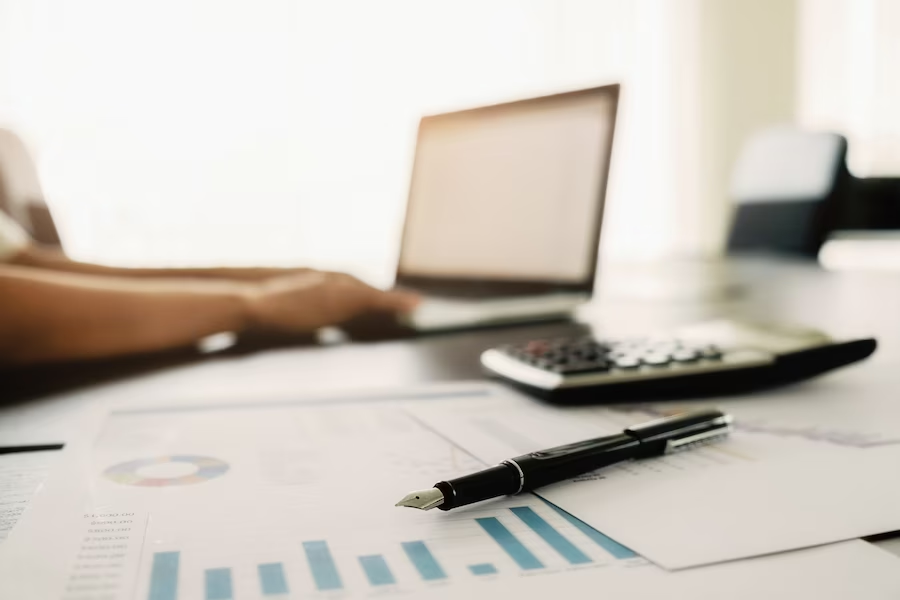
4. Preparing Documentation:
Documentation is a key component of any factory audit. Preparing all necessary documentation, including manufacturing records, safety and quality control reports, and environmental sustainability reports, is important. This documentation should be organized and easily accessible to auditors.
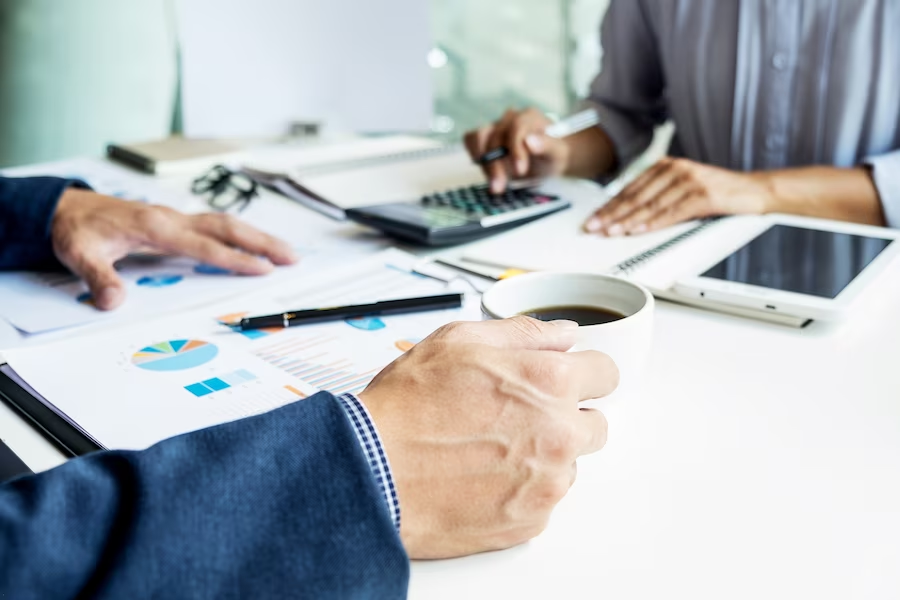
5. Conducting Mock Audits:
Conducting mock audits can be a helpful way to identify any areas of weakness or non-compliance before an external audit. This involves simulating an audit and reviewing your manufacturing processes and documentation to identify improvement areas. By conducting mock audits, you can proactively address any issues and ensure you are fully prepared for an external audit.
By following these key steps, custom plush toy manufacturers can effectively prepare for a factory audit and demonstrate their commitment to meeting high standards and achieving compliance. A successful factory audit can help build customer and vendor trust and ensure the long-term success of your custom stuffed with business.
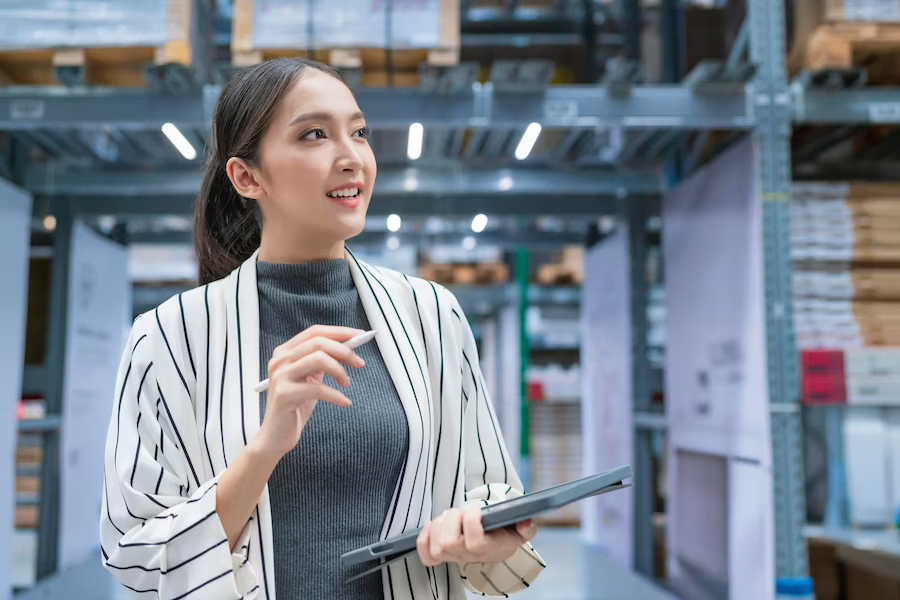
VI. Conclusion
In conclusion, factory audits are essential to ensuring the quality and trustworthiness of custom plush toy manufacturers. They provide buyers with a comprehensive understanding of the manufacturer’s practices, compliance, and quality control systems.
By undergoing a factory audit, manufacturers can demonstrate their commitment to ethical and safe manufacturing practices and assure their clients of their capabilities.
It is crucial for custom plush toy manufacturers to be transparent and upfront with their buyers about their compliance and quality control systems.
By doing so, manufacturers can establish themselves as trustworthy and reliable client partners. Furthermore, they can use the audit results to identify areas for improvement and implement measures to enhance their operations.
Demonstrating compliance, ethical manufacturing practices, and consistent quality of service is vital in a highly competitive market. Factory audits provide a powerful tool for custom plush toy manufacturers to establish themselves as industry leaders and meet the demands of their clients. By investing in regular audits, manufacturers can ensure the long-term success of their business while providing their clients with high-quality, safe, and reliable products and services.