I. Introduction
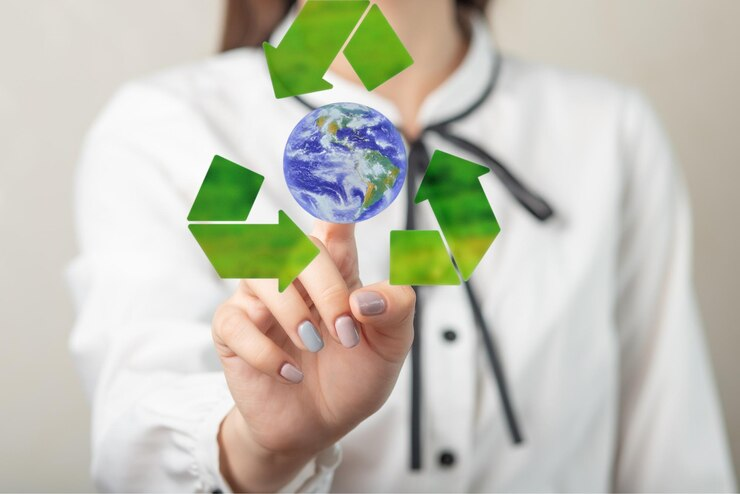
As the demand for environmentally friendly and sustainable products continues to grow, more and more companies in the plush toy industry are turning to recycled materials to create their products. However, ensuring the quality and credibility of recycled materials can be a challenge. This is where the Global Recycled Standard (GRS) comes in.
The GRS is a third-party certification that sets requirements for the use of recycled materials in products, including plush toys and fabrics. It ensures that the entire supply chain, from sourcing recycled materials to the manufacturing process and final product, meets strict social and environmental practices and chemical restrictions.
In this complete guide to GRS certification for recycled plush toys, we will cover everything you need to know about this important certification, including its history and development, the certification process, and the benefits it provides for both manufacturers and consumers.
By the end of this guide, you will have a thorough understanding of GRS certification, and be equipped with the knowledge you need to make informed decisions about your plush toy sourcing, production, and supply chain.
II. What is GRS Certification?
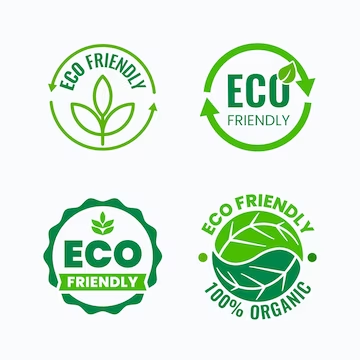
The Global Recycle Standard (GRS) is a third-party certification program that sets requirements for the processing, manufacturing, and verification of recycled materials. It was developed by Textile Exchange, a global nonprofit organization that promotes sustainability in the textile industry. GRS certification ensures that the entire supply chain of a product, from raw material suppliers to the final product, meets strict social and environmental practices.
GRS is a comprehensive certification program that covers all aspects of recycled material production, from chemical restrictions to supply chain transparency. The certification process includes a third-party audit of the manufacturing process, verifying that the recycled material is processed and managed according to environmental practices and chemical restrictions.
The certification sets requirements for third-party certification of recycled content, a chain of custody, social and environmental practices, and chemical impacts. It also includes pre-consumer and post-consumer recycled material and requires that stakeholders are engaged throughout the supply chain.
GRS certification is a credible certification that verifies the authenticity of recycled claims and ensures that the recycled material used in production meets environmental requirements. It helps companies create a more sustainable supply chain by using certified recycled materials and improving the quality of the final product.
In the next section, we will explore the difference between GRS and RCS certification.
III. GRS vs RCS Certification
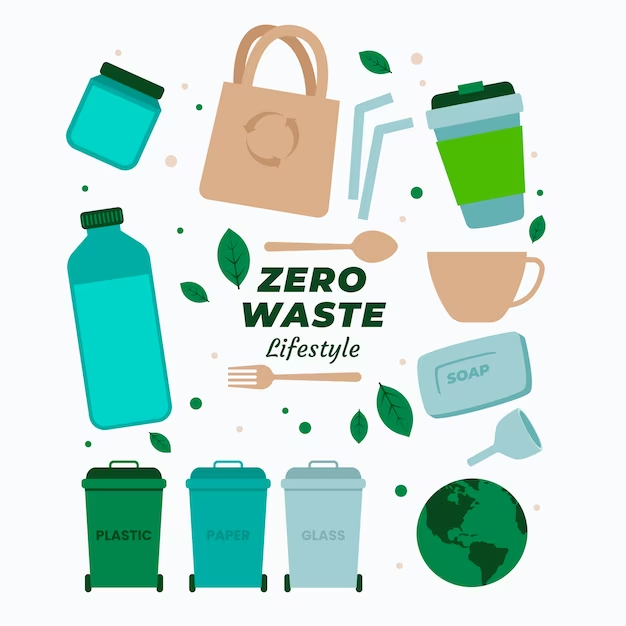
While GRS and RCS are both certifications for recycled materials, there are some differences between the two.
GRS is a certification for products that are made from recycled materials and sets requirements for third-party certification of recycled content, chemical restrictions, custody social and environmental practices, and social and environmental practices throughout the manufacturing process. On the other hand, RCS (Recycled Claim Standard) only certifies the recycled content of a final product, which means that the product must contain a certain percentage of recycled material.
Another difference between GRS and RCS is the level of supply chain traceability required. GRS requires a higher level of traceability and sets a strict chain of custody requirements for both pre-consumer and post-consumer recycled materials. This ensures that the recycled material used in the final product is tracked and verified at each stage of the supply chain.
GRS is also considered to be a more credible certification, as it is developed by Textile Exchange, a non-profit organization dedicated to sustainability in the textile industry. In contrast, RCS is a certification developed by the Global Recycled Standard (GRS) organization, which focuses primarily on setting standards for recycled plastics.
Ultimately, the choice between GRS and RCS certification depends on the specific needs and goals of the company or brand seeking certification. For those looking to demonstrate a commitment to responsible production and environmental practices, GRS certification is often the preferred choice due to its more comprehensive requirements and a higher level of traceability.
IV. Environmental Requirements for GRS Certification
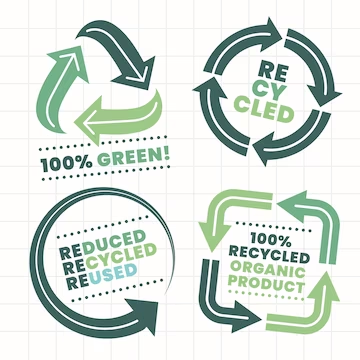
The GRS sets strict environmental requirements for certification to ensure that the manufacturing process of recycled plush toys is environmentally responsible. These requirements cover various aspects of the supply chain, from the sourcing of raw materials to the final product.
One of the primary requirements is the use of recycled materials. The GRS requires that a minimum of 20% of the final product be made from recycled materials. This means that the plush toy must contain a significant amount or mixture of post-consumer or pre-consumer recycled content.
Additionally, the GRS requires companies to have a chain of custody system in place. This system ensures that the recycled materials used in the plush toy have been processed in an environmentally responsible way and that the intended final product is made from these materials. The chain of custody system also ensures transparency in the supply chain, allowing for the traceability of recycled content.
The GRS also sets requirements for the textile exchange standards and third-party certification of recycled content. This means that companies must verify the recycled content of their products through an independent third-party certification body. The certification body must meet strict social and environmental practices and must be accredited by the Textile Exchange.
Chemical practices and restrictions are another critical requirements of GRS certification. The GRS sets strict limits on the use of harmful chemicals in the manufacturing process, ensuring that the final product is environmentally friendly. Companies must meet these chemical restrictions and practices to receive GRS certification.
Stakeholder engagement is also essential for GRS certification. Companies must engage with their suppliers, customers, and other stakeholders to ensure that their practices and products meet GRS requirements. This engagement also ensures that stakeholders are aware of the company’s commitment to sustainability and responsible production.
Overall, the GRS sets comprehensive environmental requirements for certification, ensuring that the manufacturing process of recycled plush toys meets strict standards for sustainability and responsible production. By meeting these requirements, companies can create environmentally responsible plush toys that are credible, traceable, and environmentally friendly.
V. Benefits of GRS Certification for Recycled Plush Toys
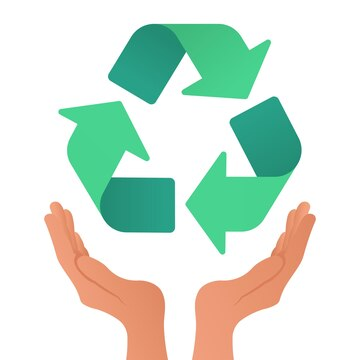
GRS certification is not only beneficial for the environment but also for businesses that manufacture recycled plush toys. Here are some of the key benefits of GRS certification:
A. Meeting Consumer Demand for Sustainable Products
As consumers become more environmentally conscious, there is a growing demand for natural and sustainable products. GRS certification ensures that recycled plush toys meet strict social and environmental practices, making them an attractive option for consumers who want to purchase environmentally friendly products.
B. Meeting Supply Chain Requirements
Many companies require their suppliers to have third-party certification of recycled content in their products. GRS certification provides assurance that the recycled content in the plush toys has been verified, allowing companies to meet supply chain requirements and work with environmentally responsible suppliers.
C. Compliance with Environmental Regulations
Manufacturing recycled plush toys with GRS certification ensures compliance with environmental regulations, including chemical practices and chemical restrictions. Compliance with these regulations is critical to avoiding harmful chemical impacts both on the environment and ensuring the safety of the final product.
D. Brand Reputation and Credibility
GRS certification helps brands and companies communicate their commitment to sustainable and responsible production. Having a GRS certification demonstrates that the company takes the necessary steps to manage its resources and production processes in an environmentally responsible way. This can help enhance brand reputation and credibility with customers and stakeholders.
E. Improved Stakeholder Engagement
GRS certification requires stakeholder engagement throughout the supply chain, from suppliers to retailers to customers. This improved engagement can lead to better relationships between stakeholders, better supply chain management, and ultimately, better products.
F. Access to New Markets
Having a GRS certification opens up new markets for companies that manufacture recycled plush toys. Many retailers and brands require certification from credible organizations such as GRS, RCS, and Textile Exchange Standards. GRS certification can give manufacturers access to these markets, increasing sales and revenue.
Overall, GRS certification sets requirements for third-party certification of recycled content in the manufacturing process of recycled plush toys, ensuring compliance with environmental requirements, improving supply chain management, enhancing brand reputation and credibility, and ultimately increasing access to new markets.
VI. How to Get GRS Certification
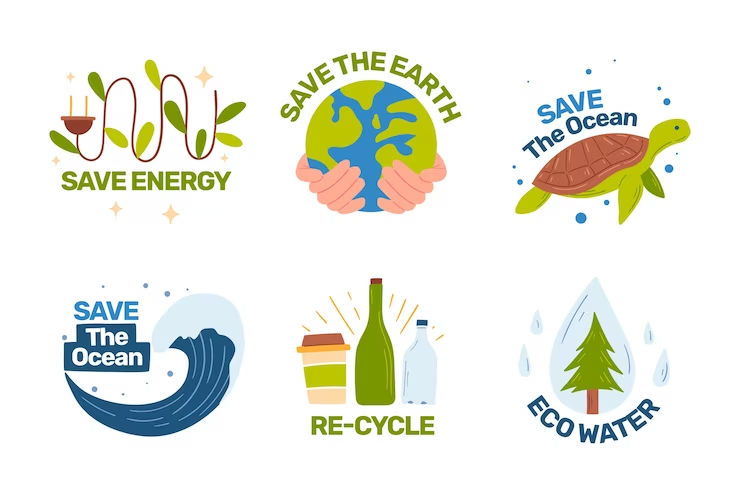
To obtain GRS certification for recycled plush toys, manufacturers need to go through a series of steps and meet certain requirements. Here are the steps involved in the GRS certification process:
1. Review the GRS certification requirements:
The first step is to review the GRS certification requirements to ensure that your manufacturing process meets the standards set by the certification body.
2. Choose a third-party certification body:
There are several third-party certification bodies accredited by GRS that manufacturers can choose from. Some of the top options include Control Union Certifications, Ecocert, Textile Exchange, Global Organic Textile Standard (GOTS), Intertek, TÜV Rheinland, and SGS. It’s important for manufacturers to choose a certification body that has experience in the textile and plush toy industries and is knowledgeable about the GRS requirements and auditing process. Additionally, it’s important to consider the cost and location of the certification body, as well as its reputation for providing reliable and thorough audits.
3. Prepare for the audit:
Manufacturers need to prepare for the audit by providing documentation on their supply chain, manufacturing process, and other relevant information. The certification body will review the documents and conduct an on-site audit of the manufacturing facility.
4. Conduct the audit:
The certification body will conduct an on-site audit to assess the manufacturer’s compliance with the GRS standards. The audit will cover areas such as supply chain, chemical management, and social and environmental practices.
5. Receive the GRS certificate:
If the manufacturer meets all the requirements, the certification body will issue the GRS certificate, which is valid for one year. The manufacturer needs to renew the certificate annually to maintain GRS certification.
6. Verify the GRS certificate:
To ensure the credibility of the GRS certificate, customers and stakeholders can verify the certificate on the GRS website.
Overall, the GRS certification process can be challenging and time-consuming, but it is crucial for manufacturers looking to produce high-quality recycled plush toys and meet the increasing demand for environmentally sustainable products.
VII. Costs of GRS Certification
The cost of obtaining GRS certification can vary depending on various factors such as the size of the company, the complexity of the supply chain, and the number of sites seeking certification. The certification cost also includes the cost of audits, testing, and ongoing maintenance.
Typically, the certification process includes an initial registration fee and an annual certification fee. The registration fee can range from a few hundred to several thousand dollars, while the annual fee ranges from a few hundred to several thousand dollars, depending on the size and complexity of the supply chain.
Additionally, companies seeking GRS certification may incur additional costs related to upgrading their production processes and supply chains to meet the standard requirements. These costs can include investments in new equipment, changes to manufacturing processes, and training for employees.
Despite the costs associated with GRS certification, the benefits of certification can ultimately outweigh the initial investment. Certification can help companies demonstrate their commitment to sustainability and environmentally friendly business practices, leading to increased consumer trust and loyalty. Additionally, GRS certification can help companies gain access to new markets and customers who prioritize sustainability in their purchasing decisions.
It is important to note that the cost of GRS certification should be viewed as an investment in the long-term sustainability and success of a company rather than a short-term expense.
VIII. Conclusion
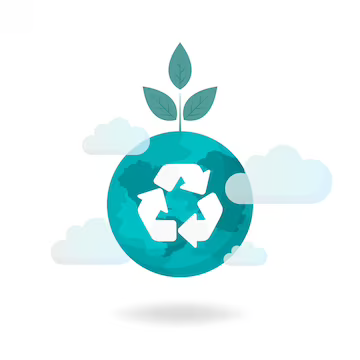
In conclusion, the Global Recycled Standard (GRS) is a third-party certification that sets strict minimum social and environmental requirements for recycled materials and their supply chain. GRS certification provides assurance to customers that their plush toys are made with environmentally friendly practices and chemical restrictions, and that the manufacturing process is managed responsibly.
Obtaining GRS certification is an important step for companies that want to create environmentally sustainable products and meet the demands of customers who value sustainability. By investing in GRS certification, companies can verify their recycled content claims, reduce the harmful impact of plastics and other materials on the environment, and ensure transparency and credibility throughout their supply chain.
While the costs of GRS certification may vary depending on factors such as company size, product complexity, and location, the benefits of certification can outweigh the costs in the long run. Companies that obtain GRS certification can gain a competitive advantage in the marketplace and attract customers who value sustainability and responsible production practices.
Overall, GRS certification is a valuable tool for companies that want to create high-quality and sustainable soft plush toys while reducing their environmental footprint. By adhering to the rigorous standards set by GRS, companies can demonstrate their commitment to sustainability, responsibility, and transparency, and contribute to a more sustainable future for our planet.